How Can We Help?
What is E-Cam?

Question
JTEKT Electronics servos have a function called an electronic cam.
What is it?

Answer
E-Cam is an abbreviation for Electric Cam.
This function allows the slave axis to operate in accordance with the movement of the master axis.
In a normal servo system, a motion controller is provided for each master axis and slave axis.
In comparison, JTEKT Electronics’ servo systems connect and control the rotation signal of the master axis to the servo driver for the slave axis, so there is no need for a motion controller for the slave axis.
For setting the servo driver for the slave axis, see the steps below.
Rough steps
1. Set the pulse signal from the master axis.
2. Set the clutch engagement timing.
3. Set the gear ratio of the master axis.
4. Set the positional relationship of the E-Cam curves (master and slave).
5. Set the gear ratio of the slave axis.
6. Configure operation settings in PR mode.
2. Set the clutch engagement timing.
3. Set the gear ratio of the master axis.
4. Set the positional relationship of the E-Cam curves (master and slave).
5. Set the gear ratio of the slave axis.
6. Configure operation settings in PR mode.
Setup steps
Let’s operate the E-Cam using a simple operation as shown below.
Master axis: The signal from the encoder connected to CN5 is the master axis.
Clutch engagement timing: Controlled by DI input.
Gear ratio: 1:1 One revolution of the master axis makes the slave axis one revolution.
E-Cam curve: straight line. (Same operation as master axis)
Master axis: The signal from the encoder connected to CN5 is the master axis.
Clutch engagement timing: Controlled by DI input.
Gear ratio: 1:1 One revolution of the master axis makes the slave axis one revolution.
E-Cam curve: straight line. (Same operation as master axis)
Mode Setting
E-Cams are supported in “PR mode”.
Set P1.001 to 0x0001 on the KSD-Soft “Parameter Editor” screen.
(If you want to rotate the slave axis in the reverse direction, set it to 0x0101.)
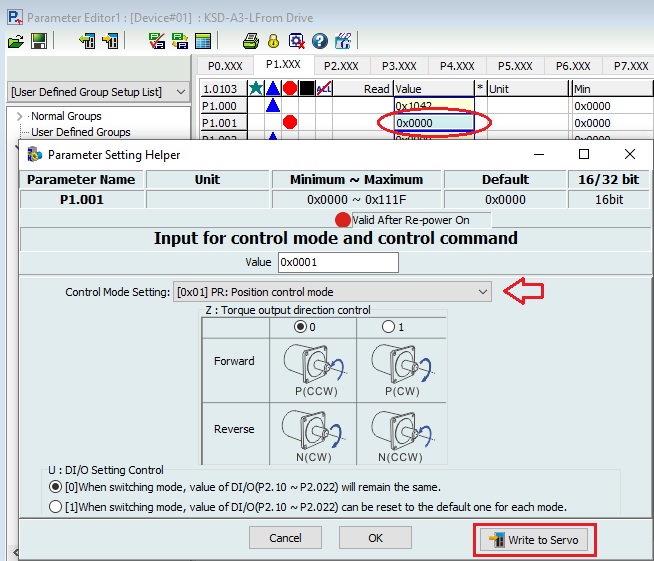
* The settings will become effective when the servo driver is powered on again.
Set P1.001 to 0x0001 on the KSD-Soft “Parameter Editor” screen.
(If you want to rotate the slave axis in the reverse direction, set it to 0x0101.)
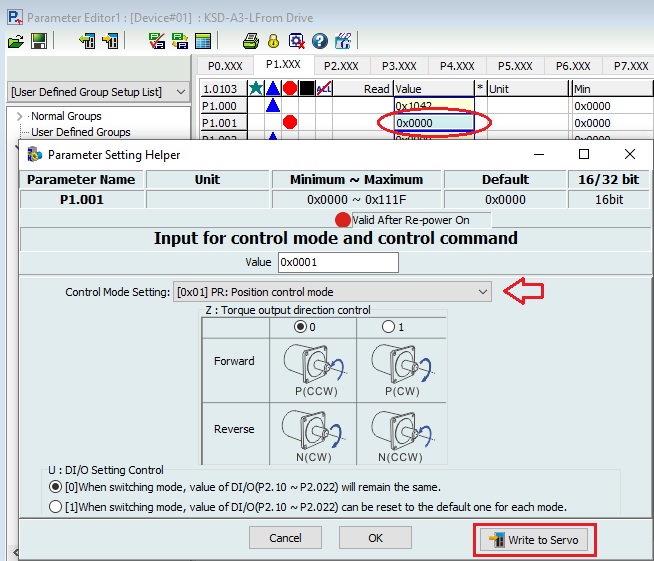
* The settings will become effective when the servo driver is powered on again.
Clutch Engagement Timing
When DI6 turns ON, try clutch engagement.
Assign DI6 to “0x36:E-Cam engaging control (A contact)” on the “Digital IO/Jog Control” screen of KSD-Soft.
Assign DI6 to “0x36:E-Cam engaging control (A contact)” on the “Digital IO/Jog Control” screen of KSD-Soft.
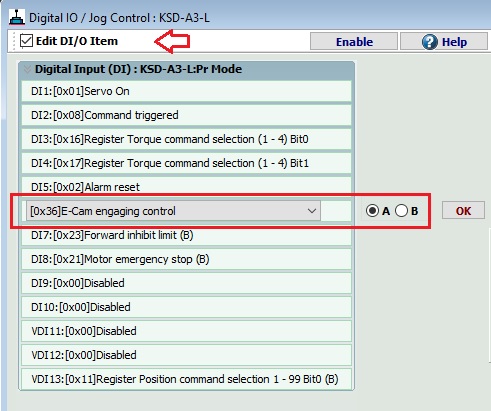
Master Axis Axis Ratio
In this example, we assume that a 100P/R encoder is connected to the master axis.
On the KSD-Soft “Parameter Editor” screen, set P5.083 to 1 and P5.084 to 400.
(For 100P/R, set 4 times that value to P5.084)
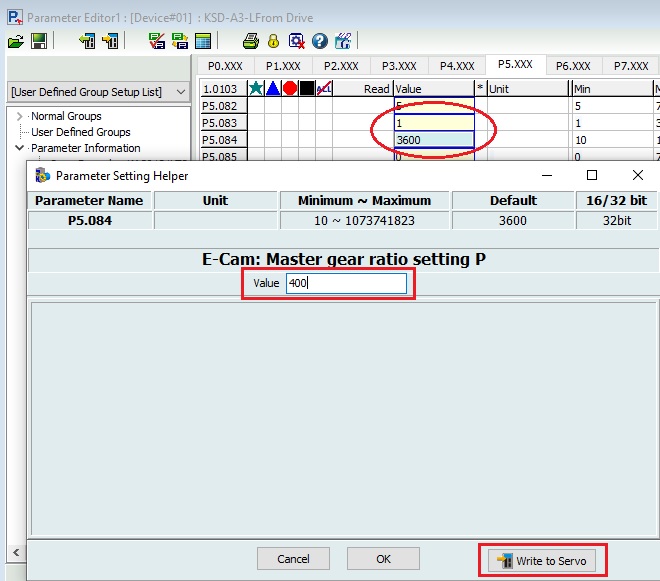
* If you want the slave axis to rotate once for every two rotations of the master axis, set P5.084 to double 800.
On the KSD-Soft “Parameter Editor” screen, set P5.083 to 1 and P5.084 to 400.
(For 100P/R, set 4 times that value to P5.084)
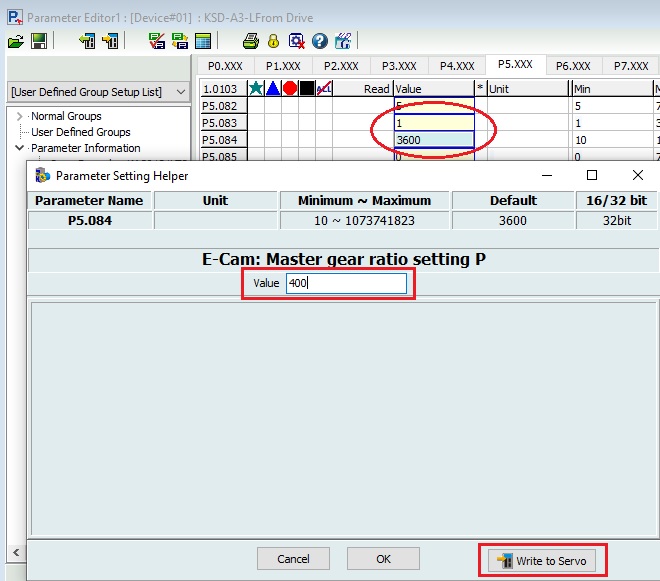
* If you want the slave axis to rotate once for every two rotations of the master axis, set P5.084 to double 800.
Slave Axis Gear Ratio
In this example, the denominator is 100000 and the numerator is 16777216.
On the KSD-Soft “Parameter Editor” screen, set P1.044 to 16777216 and P1.045 to 100000.
On the KSD-Soft “Parameter Editor” screen, set P1.044 to 16777216 and P1.045 to 100000.
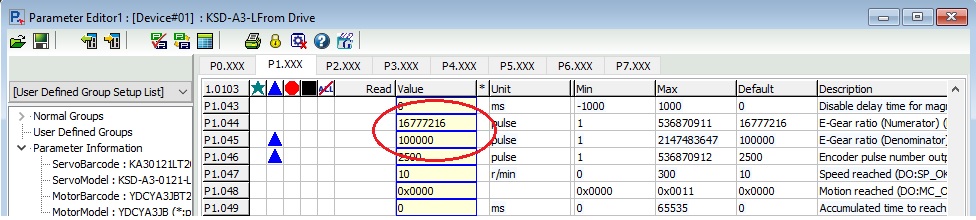
E-Cam Curve
In this example, one revolution of the slave axis is divided into five parts.
Set the point designation to use 5 points from his address number 100.
On the KSD-Soft “Parameter Editor” screen, set P5.081 to 100 and P5.082 to 5.
Set the point designation to use 5 points from his address number 100.
On the KSD-Soft “Parameter Editor” screen, set P5.081 to 100 and P5.082 to 5.
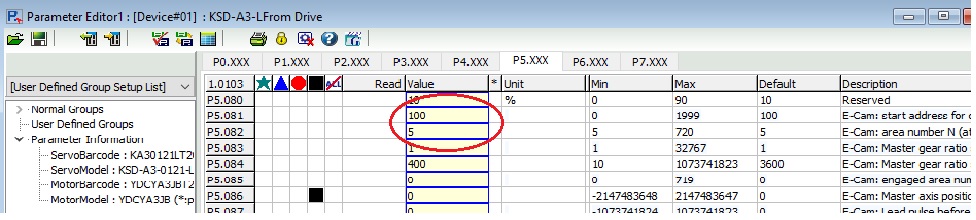
Creating an E-Cam curve
Enter directly using the “Data Array Editor” on the “High Speed Position Capture/Compare” screen of KSD-Soft.
Since the slave axis makes one rotation at 100000 PUU, enter 0,20000,40000,60000,80000,100000.
* Although the starting point 0 degrees and the ending point 360 degrees are the same point, both must be entered into the data array.
* By doing so, the mechanical cam can be rotated completely around.
* Therefore, a total of 6 pieces of data will be entered.
The cam curve looks like this:
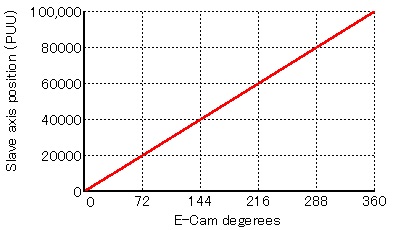
* Please perform “Write to the EEPROM” after completing “Write to Servo” for data array.
Since the slave axis makes one rotation at 100000 PUU, enter 0,20000,40000,60000,80000,100000.
* Although the starting point 0 degrees and the ending point 360 degrees are the same point, both must be entered into the data array.
* By doing so, the mechanical cam can be rotated completely around.
* Therefore, a total of 6 pieces of data will be entered.
The cam curve looks like this:
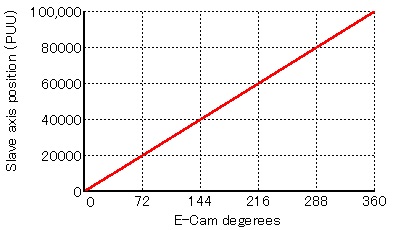
* Please perform “Write to the EEPROM” after completing “Write to Servo” for data array.
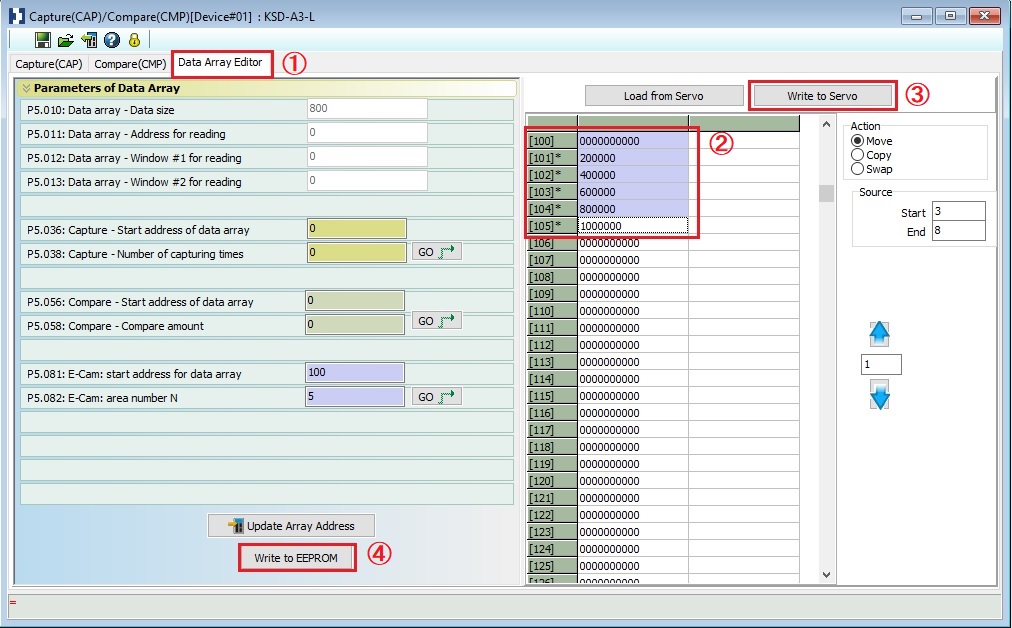
Settings for running in PR mode
Assign positioning-related signals to move in PR mode.
Set DI2, DI7, and DI8 on the “Digital IO/Jog Control” screen of KSD-Soft.
DI2 0x08: Command Triggerd
DI7 0x00: Disable
DI8 0x21: Motor emergency stop *Changed to A contact
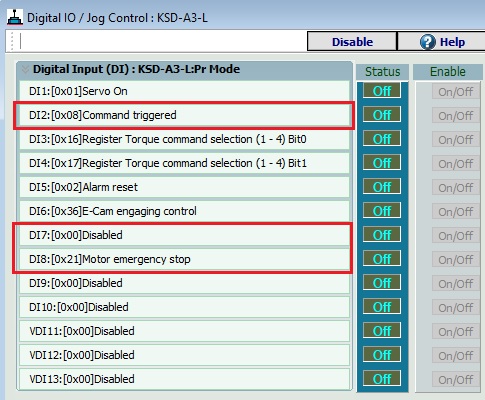
Set the E-Cam for PR #1 on the “PR Mode Setting” screen of KSD-Soft.
TYPE path setting: Set “[8]:Write to Parameter or Data Array”.
Write target: Set “0:Parameter” to P5.088.
Data: Set “Target” to 0x00001111.
*Set the cam command source (external encoder), engagement/disengagement conditions, etc.
Please perform “Write PR parameters”.
Set DI2, DI7, and DI8 on the “Digital IO/Jog Control” screen of KSD-Soft.
DI2 0x08: Command Triggerd
DI7 0x00: Disable
DI8 0x21: Motor emergency stop *Changed to A contact
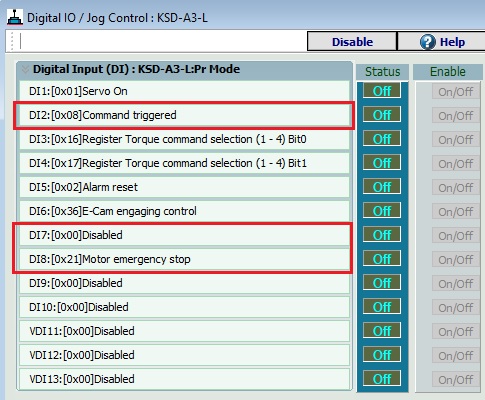
Set the E-Cam for PR #1 on the “PR Mode Setting” screen of KSD-Soft.
TYPE path setting: Set “[8]:Write to Parameter or Data Array”.
Write target: Set “0:Parameter” to P5.088.
Data: Set “Target” to 0x00001111.
*Set the cam command source (external encoder), engagement/disengagement conditions, etc.
Please perform “Write PR parameters”.
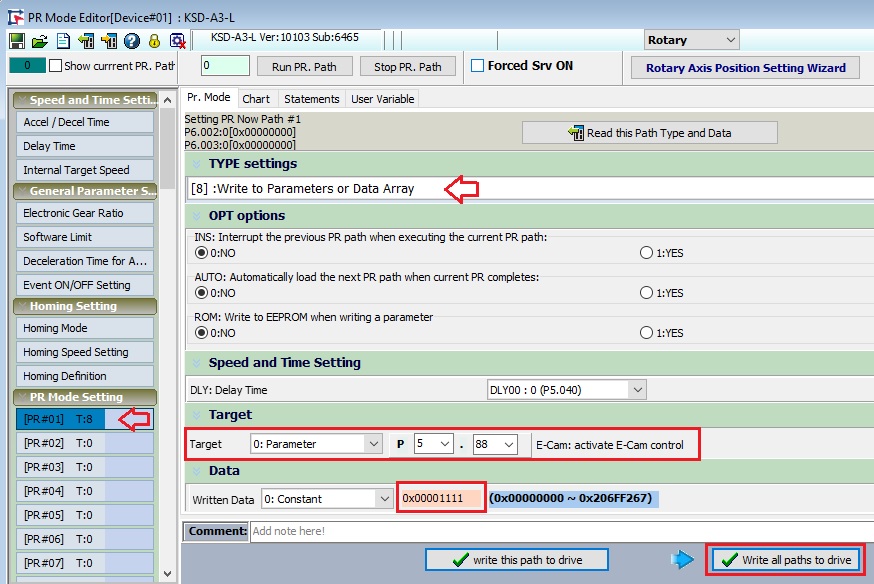
Try moving
Turn on the servo.
Execute PR #01.
Turn on E-Cam engagement using DI input.
Rotate the external encoder by hand and check how the slave axis actually moves.
Execute PR #01.
Turn on E-Cam engagement using DI input.
Rotate the external encoder by hand and check how the slave axis actually moves.
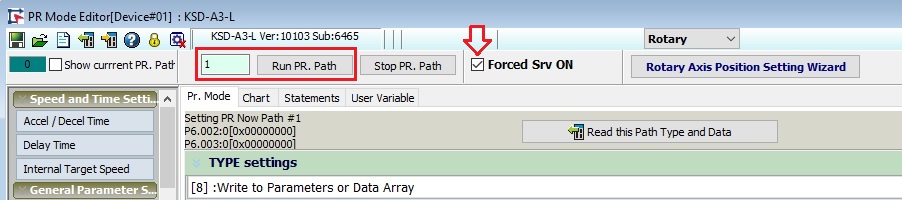
Inquiry
technical support
Click here for inquiries by email
Click here for inquiries by email